Automation is a time lapse
KW Solution has progressively evolved from a tool and mould maker into a subcontractor for individual parts and small series. The company relies on automated processes and the RS 2 robot system from HERMLE to efficiently manage high-mix, low-volume requirements.
"Without automation, we’d no longer exist," says managing director Dr Jens Buchert with confidence. In 2016, the entrepreneur took over Karl Walter Formen- und Kokillenbau GmbH & Co. KG, now known as KW Solution for short, and has made significant investments since then. "Thanks to our automation, we are able to utilise the machines to a very high degree." Each automated five-axis machining centre – C 32 U, C 52 U and C 52 MT from HERMLE – exceeds 4,000 spindle hours a year.
Karl Walter Formen- und Kokillenbau was founded in 1960 and is based in the southern German town of Göppingen. The company produces, for example, moulds for aluminium rims and cast parts for the automotive industry, ranking among the leading manufacturers in this field. Shortly after taking over the business, Dr Jens Buchert modernised and digitalised it extensively, a process that continues to this day. "I bought the company because we make wheels. And they will always be needed – I thought – whether a car runs on fossil fuels or electricity," he recalls.
"What I hadn’t anticipated was the intense Chinese competition that has emerged in this sector on Europe’s doorstep in recent years." As a result, the company now primarily manufactures individual parts and small series for various other industries. In addition to aluminium and steel, the subcontractor processes all materials, including non-ferrous metals and difficult-to-machine metals such as tungsten. KW Solution is increasingly moving away from tool and mould production. "Tool and mould making now accounts for only about ten percent of our capacity. Our core industry is gradually fading in Germany," he states.
New ideas are in high demand
The proactive entrepreneur came up with a plan B. "In my view, many of those currently exploring new business models are missing the mark. I was looking for a product that the customer ‘wants’ and that sparks desire." The result: The all-terrain DARC MONO expedition vehicle. Its base is a sturdy IVECO chassis, which KW Solution enhances with a carbon fibre cabin and a range of practical features. The customised insulation layer protects against noise and temperatures from -30 to +50 degrees Celsius. The vehicle features water and dust-resistant hatches on both sides that provide access to the interior.
Hinges and door handles, which KW Solution manufactures automatically on its C 32 U from HERMLE, are also used, for example. "Together with strategic partners, we retain large parts of the value chain in-house," explains Dr Jens Buchert. "This enables us to efficiently implement our development and the associated production processes. Actually, the DARC MONO doesn’t really suit us at all. That’s why we make it," he grins.
-
The RS 2 robot system handles the pallets and workpieces on the C 32 U machining centre. -
Thanks to automatic pallet and workpiece handling, KW Solution also produces unmanned at night. -
In addition to approximately 80 per cent individual parts, KW Solution also manufactures small series, such as door handles for its DARC MONO expedition vehicle. -
Chic, functional, robust – KW Solution machines components for the DARC MONO. -
The five-axis machining centres from Gosheim are characterised by high precision and reliable processes. -
KW Solution retains large parts of the value chain in-house. -
KW Solution’s experienced team takes care of the design, construction, development and validation of the components. -
Hinge for a window frame on the DARC MONO – machined on the C 42 U. -
The company uses the HERMLE systems to mill door handles for the DARC MONO, for example. -
The DARC MONO is an all-terrain expedition vehicle that KW Solution tailors to meet customer specifications. -
Managing director Dr Jens Buchert: "Thanks to automation with the RS 2 robot system, we were able to boost our spindle runtimes to over 4,000 hours a year." -
Dr Jens Buchert (left), managing director, and Bastian Hummel, head of automation, both KW Solution. -
KW Solution employs 25 people in Göppingen and manufactures, among other products, the DARC MONO expedition vehicle.
Always stay in sync
However, the entrepreneur not only focuses on exceptional motorhomes but also on lean processes and automation. "We need to increase productivity in Germany," he says convincingly. "Machines should run 24 hours a day – and that can only be achieved on a single shift with automation." KW Solution produces around 80 per cent of its workpieces in batch size 1. "We’ve realised that we’re not using our robot systems to full capacity. We also need small series that we use as a buffer. Because there are always times, for example, when a customer requests a change at short notice or cancels an order."
When KW Solution put the first RS 2 robot system into operation on a C 32 U in 2020, the company ventured into new territory. "That was the famous ‘jump in at the deep end’ for us," says Dr Jens Buchert. "There were no references for single-part automation at the time." KW Solution set to work together with HERMLE. "We considered how to design the machine to handle batch size 1, in particular." Clamping devices, tool holding fixtures, process sequences – no stone was left unturned. "And, of course, we also ran iteration loops to refine and get closer to the optimum," reveals Buchert. He is especially proud of his 25 employees: "They were fully committed from the start and actively supported the project."
Automation for individuality
Every clamping setup is different, and KW Solution uses specialised tools for about 30 per cent of its work. For example, the ZM 192 additional magazine supplements the 36 tools in the C 32 U, providing enough alternatives to handle all machining tasks. "If we define something incorrectly and a length is not quite right, it rattles," says Bastian Hummel, summarising the situation. The head of automation accompanied the process from the very beginning. "Our programs are collision-tested, and we’re confident that the machines will run unmanned overnight without any issues."
Nevertheless, a component such as a sensor can always fail. "The average spindle runtime of machines without automation is around 1,600 hours per year, whereas with our robot system, it’s about three times that," explains Dr Jens Buchert. "Automation is therefore a kind of time lapse." Bastian Hummel adds: "The service from HERMLE is excellent; many issues can be resolved over the phone with the application technology team. If needed, the spare part and fitter are with us by the next day at the latest, and the machine is back up and running in next to no time."
KW Solution is already planning the next expansion. "We want to connect another machining centre to the existing RS 2 robot system with the C 32 U," says Dr Jens Buchert. "We have ideas for new components that we need for our own products. To achieve this, we need more capacity."
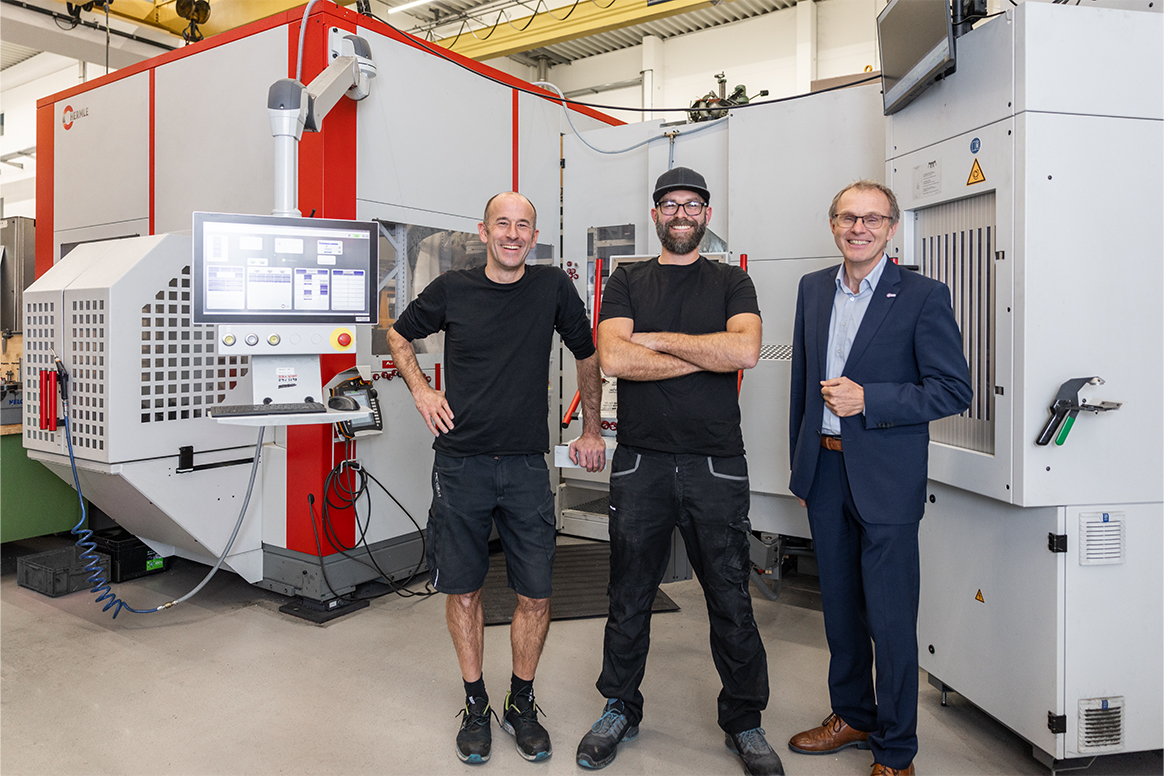